Fasteners and Machining: Incorporating Precision and Stamina in Production
Fasteners and Machining: Incorporating Precision and Stamina in Production
Blog Article
Mastering the Art of Bolts and Machining: Innovations and Finest Practices
In the realm of commercial manufacturing and design, the mastery of fasteners and machining is a foundation of ensuring architectural integrity, capability, and longevity in various applications. Join us as we explore the newest innovations and dig into the nuanced world of mastering bolts and machining, discovering vital understandings and strategies that can raise your technique to design services.
Development of Attachment Technologies
Throughout the commercial transformation and into the contemporary age, the development of fastening modern technologies has been noted by constant improvements in effectiveness and integrity. Fasteners, such as bolts, rivets, and screws, play an essential duty in various sectors, including vehicle, aerospace, building and construction, and electronics. The demand for more powerful, much more durable, and easier-to-install fastening options has actually driven technology in the area.
One significant growth has actually been the change towards accuracy machining methods to create fasteners with greater resistances and premium performance. This shift has allowed makers to create bolts that fulfill stringent high quality requirements and deal enhanced resistance to corrosion and exhaustion.
Furthermore, the introduction of sophisticated products, such as titanium alloys and composites, has changed the abilities of fasteners. Fasteners and Machining. These products supply remarkable strength-to-weight proportions, making them excellent for applications where decreasing weight is essential without compromising architectural stability
Advancements in Machining Techniques
In the realm of commercial production, the constant development of machining approaches has led the way for extraordinary accuracy and performance in the production of fasteners. Among the substantial improvements in machining techniques is the utilization of Computer system Numerical Control (CNC) technology. CNC equipments use unmatched precision and repeatability by permitting automated control of machining tools. This precise control enables producers to create complex and intricate bolt styles easily.
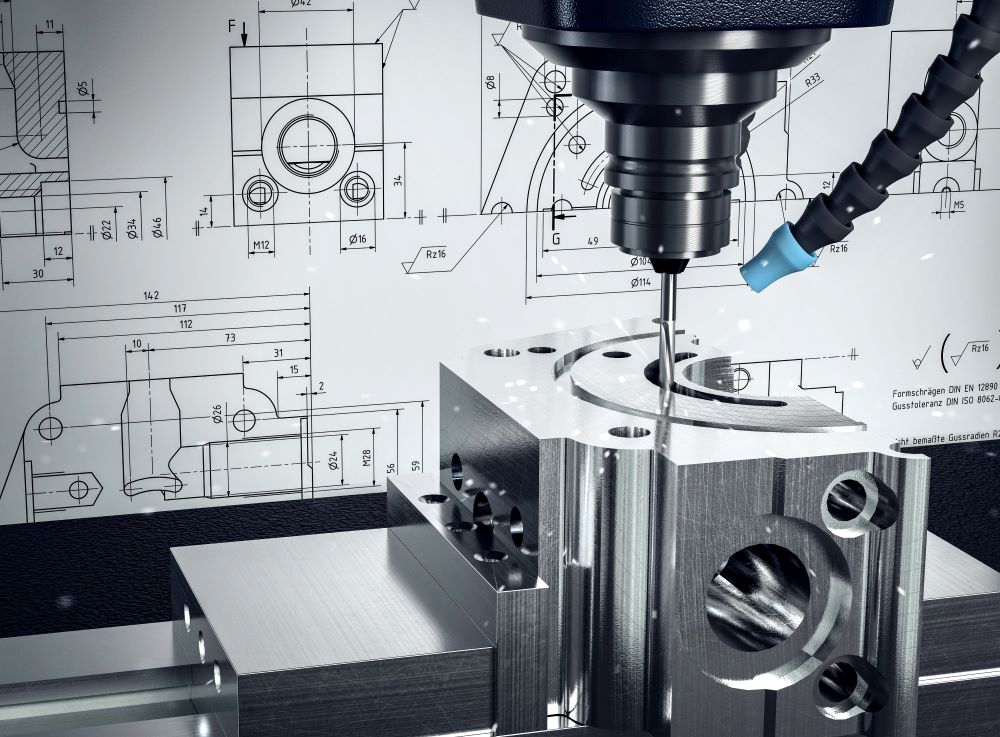
Additionally, the adoption of multi-axis machining facilities has made it possible for simultaneous reducing procedures from various angles, better enhancing efficiency and decreasing production times. By utilizing these sophisticated machining methods, manufacturers can fulfill the raising demand for high-quality fasteners while maintaining cost-effectiveness in their procedures.
Selecting the Right Fastener Materials
Choosing the appropriate material for fasteners is a vital choice that substantially influences the performance and durability of the constructed parts. When picking the appropriate fastener product, numerous aspects need to be taken into consideration to make certain the longevity and dependability of the end product. image source The material picked must be compatible with the environmental conditions the fasteners will be exposed to, such as temperature variations, wetness degrees, and harsh components.
Common products utilized for bolts include stainless steel, carbon aluminum, steel, and titanium, each offering special buildings that match different applications. Stainless-steel, as an example, is known for its rust resistance, making it ideal for outdoor or marine environments. Carbon steel is an economical option ideal for numerous general-purpose applications. Aluminum is lightweight and frequently used in sectors where weight is a crucial factor. Titanium, on the various other hand, is corrosion-resistant and extremely strong, making it suitable for high-performance applications.
Enhancing Precision in Machining
Attaining ideal accuracy in machining is important for ensuring the quality and performance of machined parts. Precision in machining describes the ability to consistently produce components within tight resistances and with high precision. To improve precision in machining, producers use a variety of innovative strategies and technologies. One trick approach is utilizing Computer system Numerical Control (CNC) makers, which use premium precision have a peek here and repeatability compared to typical manual machining approaches. CNC equipments are programmable and can implement complicated machining operations with minimal human treatment, causing higher precision levels.
Along with CNC machining, the usage of innovative cutting tools and device holders can additionally substantially boost accuracy. High-grade cutting devices with advanced coverings lower see here now friction and wear, resulting in more precise cuts and dimensional precision. Applying rigid quality control steps throughout the machining procedure, such as routine evaluations and calibration of devices, assists keep constant accuracy degrees. By focusing on precision in machining, makers can accomplish exceptional item quality, tighter tolerances, and improved total efficiency of machined components.
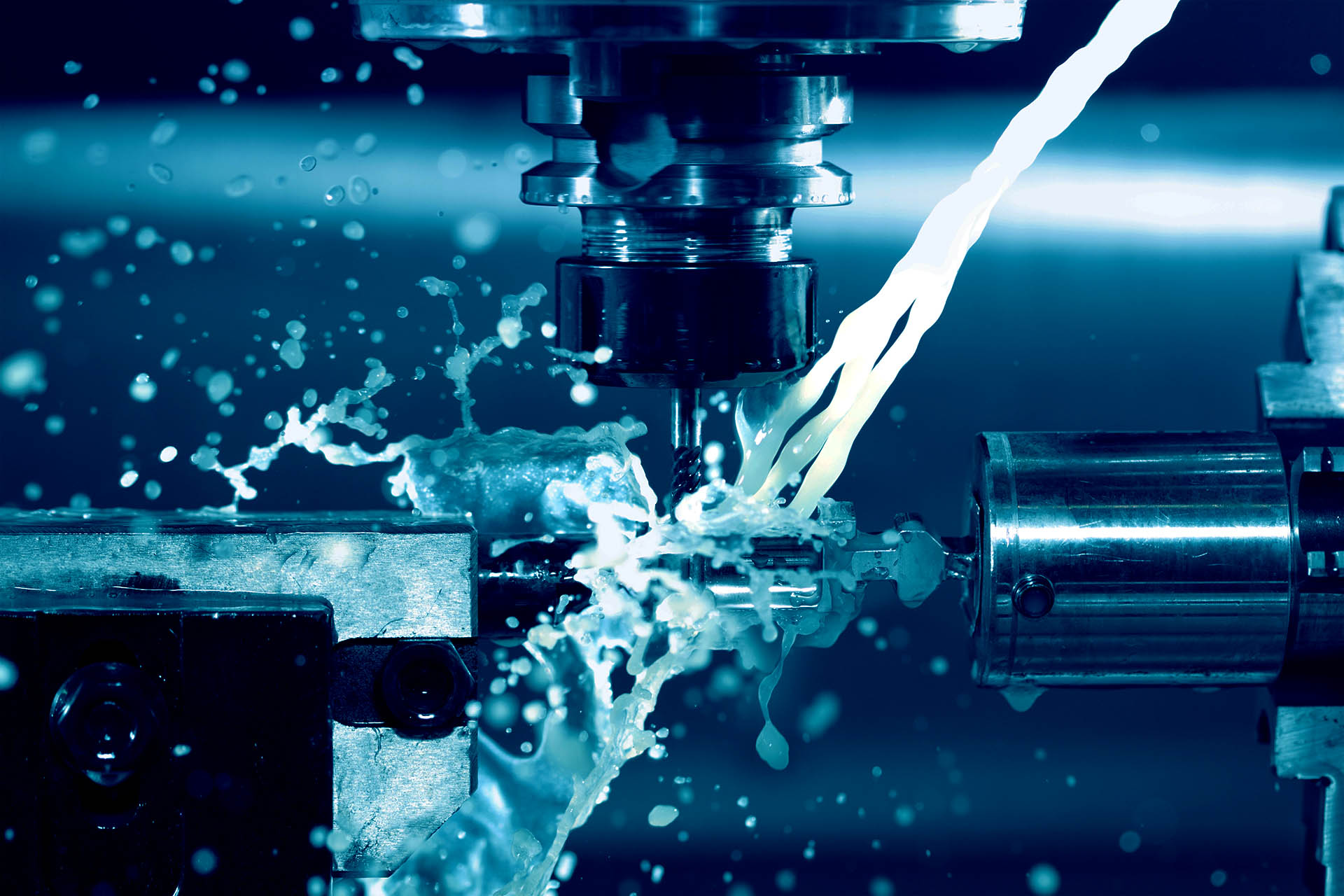
Ideal Practices for Fastener Installment
Precision in machining plays a vital duty in making certain the dependability and longevity of bolt setups. When it pertains to best methods for fastener installment, one essential element is the appropriate choice of fasteners based on the specific application needs. Utilizing the right type, dimension, and product of fastener is vital to guarantee optimal performance and longevity. Fasteners and Machining. In addition, it is vital to follow supplier standards and recommended torque worths throughout the setup procedure to avoid over-tightening or under-tightening, which can cause premature bolt failing.
Furthermore, making certain that the fastener threads are clean and free of particles before installment is vital to attaining a safe and secure and effective link. Making use of thread-locking compounds or washers can likewise improve the stability of the fastener setting up. Normal evaluations and upkeep of fasteners post-installation are recommended to identify any kind of possible concerns beforehand and prevent pricey repair services or replacements in the future. By sticking to these ideal practices, producers can maximize the integrity and efficiency of their bolt setups.
Final Thought
By selecting the right bolt materials and improving accuracy in machining, producers can accomplish optimal outcomes in their procedures. Generally, understanding the art of bolts and machining involves continual advancement and adherence to finest practices.
In the realm of commercial manufacturing, the continuous advancement of machining approaches has paved the means for unmatched accuracy and efficiency in the production of bolts.Precision in machining plays a critical function in making sure the dependability and longevity of fastener setups. When it comes to finest techniques for bolt setup, one essential facet is the appropriate choice of bolts based on the specific application needs. By choosing the best fastener materials and boosting accuracy in machining, manufacturers can accomplish ideal outcomes in their procedures. On the whole, mastering the art of fasteners and machining includes constant advancement and adherence to finest methods.
Report this page